What is JIT Inventory Management?
Just-In-Time (JIT) is an inventory management approach that aims to minimize inventory carrying costs while ensuring that materials and products are available when needed for production or customer demand. JIT focuses on efficiency and waste reduction by closely aligning inventory levels with actual demand.
What Are the Principles of JIT Inventory?
Here are the key principles and strategies associated with JIT inventory management:
- Demand-Driven: JIT relies on accurate demand forecasting and customer orders to trigger production and replenishment of inventory. Production is initiated only when there is a confirmed demand.
- Small Batch Sizes: JIT encourages producing goods in small, manageable batches. This reduces the need for large storage areas and minimizes the risk of overproduction.
- Continuous Improvement: JIT emphasizes a culture of continuous improvement, such as the use of Lean principles, to eliminate waste, reduce lead times, and enhance overall operational efficiency.
- Supplier Relationships: Strong partnerships with reliable suppliers are crucial. Suppliers are expected to deliver materials and components just in time to meet production schedules.
- Kanban System: The Kanban system is often used in JIT. It involves the use of visual cues (e.g., cards or signals) to signal when inventory needs replenishment. This helps maintain the right inventory levels without excess.
- Reduced Lead Times: Efforts are made to minimize lead times throughout the supply chain, from ordering raw materials to delivering finished products to customers.
- Quality Control: High-quality standards are essential in JIT to prevent defects and rework, which can disrupt the production process and increase costs.
- Flexible Workforce: A flexible and cross-trained workforce is necessary to handle varying production requirements and adapt to changes in demand.
- Just-in-Time Warehousing: Inventory storage is minimized, and goods are stored for the shortest time possible. This reduces holding costs and the risk of obsolescence.
- Pull System: JIT operates on a pull system, meaning that production is driven by actual customer demand. Products are pulled through the supply chain rather than pushed based on forecasts.
- Safety Stock Minimization: Safety stock (buffer stock) is kept to a minimum, only to account for unexpected variations in demand or supply disruptions.
- Continuous Monitoring: Ongoing monitoring of inventory levels, production processes, and supplier performance is essential to make real-time adjustments and improvements.
- Employee Involvement: Employee involvement and empowerment are encouraged to identify and address issues related to efficiency and quality.
How to implement JIT in Inventory?
Implementing JIT requires careful planning, effective communication, and a commitment to continuous improvement. While JIT can lead to significant cost savings and increased efficiency, it also involves some risks, such as vulnerability to supply chain disruptions when relying on a small buffer stock. Therefore, it’s crucial to assess the suitability of JIT for your specific industry and operational context before implementing it.
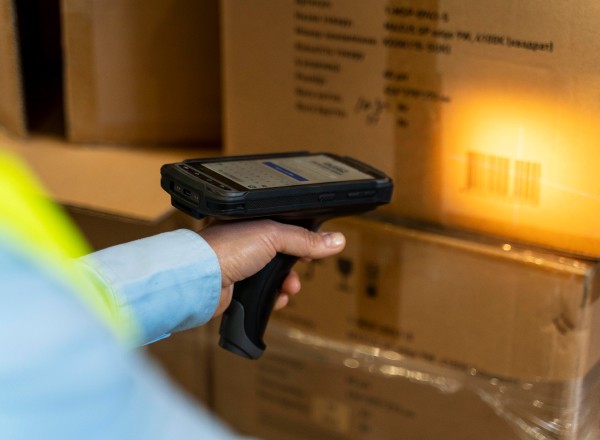
Looking for Inventory Management Software?
Read this amazing post from our partner.
Implementing Just-In-Time (JIT) inventory management involves a structured approach and careful planning. Here are the steps to implement JIT effectively:
- Assess Current Inventory Practices: Begin by evaluating your current inventory management practices. Understand your existing inventory levels, ordering processes, lead times, and associated costs. Identify areas of waste and inefficiency.
- Set Clear Objectives: Define clear and measurable objectives for implementing JIT. Common objectives include reducing carrying costs, minimizing waste, improving production efficiency, and enhancing customer service.
- Demand Forecasting: Accurate demand forecasting is crucial for JIT. Use historical data, market analysis, and customer feedback to forecast demand as accurately as possible. This will help you determine the right inventory levels.
- Supplier Collaboration: Collaborate closely with your suppliers. Establish strong relationships and communicate your JIT requirements. Ensure suppliers can deliver materials and components on time and in the required quantities.
- Kanban System: Implement a Kanban system or a similar visual control system to signal when to reorder or produce items. Kanban cards or electronic signals can help manage inventory levels effectively.
- Reduce Batch Sizes: Aim to reduce batch sizes to minimize overproduction and excess inventory. Smaller batches enable more frequent production runs and can improve flexibility.
- Streamline Processes: Streamline production and order processing processes to reduce lead times. Eliminate bottlenecks and inefficiencies wherever possible.
- Quality Control: Emphasize quality control to prevent defects and rework, which can disrupt the JIT process. Implement rigorous quality standards and practices.
- Cross-Train Employees: Develop a cross-trained and flexible workforce capable of handling various tasks and adapting to changing production requirements.
- Just-in-Time Warehousing: Reconfigure your warehousing practices to align with JIT principles. Reduce storage space, organize items for easy access, and implement efficient order picking and shipping processes.
JIT Inventory Management Techniques
- Safety Stock Management: Minimize safety stock while ensuring that you have enough buffer to handle unexpected demand fluctuations or supply disruptions. The level of safety stock should be based on data and analysis.
- Continuous Improvement: Foster a culture of continuous improvement. Encourage employees at all levels to identify and address issues related to efficiency and quality. Regularly review and optimize processes.
- Technology and Automation: Implement inventory management software and automation tools to help monitor inventory levels, track demand, and manage orders more efficiently.
- Monitor and Adjust: Continuously monitor inventory levels, supplier performance, and demand patterns. Be prepared to make real-time adjustments to avoid stockouts or overstock situations.
- Training and Education: Provide training and education to employees to ensure they understand the JIT principles and their roles in its successful implementation.
- Risk Mitigation: Develop contingency plans to manage potential risks associated with JIT, such as supply chain disruptions or unexpected demand spikes.
- Measure Performance: Establish key performance indicators (KPIs) to measure the success of your JIT implementation. Track metrics like inventory turnover, on-time delivery, and cost reductions.
- Feedback Loop: Maintain open channels for feedback and collaboration with employees, suppliers, and customers. Use feedback to continuously improve your JIT processes.
Implementing JIT is a gradual process that requires commitment and ongoing effort. Start with a pilot project or a specific product line to gain experience and then expand the JIT approach to other areas of your inventory management. Regularly assess your progress and make adjustments as needed to achieve your JIT goals.
One thought on “Just-In-Time (JIT) Inventory management”
Comments are closed.